By Inès Magoum
In addition to the prevention, reduction, recycling and reuse of waste prescribed in the United Nations (UN) twelfth Sustainable Development Goal (SDG 12) to reduce pollution by 2030, there is technological innovation. And why? Because innovation increases recovery performance and therefore results. The most advanced innovations in solid waste management include modular pyrolysis, anaerobic digestion, dry fermentation and bioconversion. These solutions are coming to Africa.
“A company that does not constantly innovate is one that exacerbates its strengths”. These are the words of Hamed Beheshti, co-founder and CEO of German company Boreal Light, which specialises in solar-powered water treatment solutions, in an interview with AFRIK 21. This principle also applies to waste.
As well as boosting the efficiency of a company or a country’s public services, the aim is really to enhance the environmental, social and even economic impact of the action to be taken. Because waste is a source of wealth. This is the leitmotiv of Honeywell, which has launched its new solid waste management technology, UpCycle Process, in 2021. “The process (…) is based on pyrolysis, which uses heat in the absence of oxygen to break down polymers, as well as molecular conversion and contaminant management. The aim is to convert plastic waste that is difficult to recycle, such as coloured, flexible and multi-coloured packaging and polystyrene, into new plastic products”, says the American supplier of plastic waste recycling solutions.
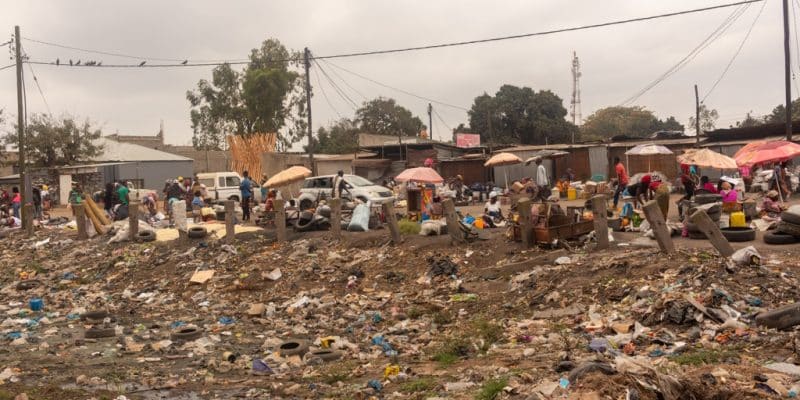
Recycling three times as much used plastic
Egyptian company Environ Adapt for Recycling Industries will be the first in Africa to benefit from Honeywell’s UpCycle Process technology. The partnership agreement was signed in November 2022 between the two parties.
Pyrolysis, anaerobic digestion, dry fermentation. ways to clean up pollution in Africa©Honeywell
Honeywell recycles plastic waste©Honeywell
Combined with other chemical and mechanical recycling processes, and with collection and sorting improvements in Egypt, UpCycle Process technology could increase the amount of waste that can be recycled to 90% – three times more than standard technology such as the pyrolysis technology used by technology solutions provider Clean Seas to convert waste into electricity in the Democratic Republic of Congo (DRC) or by Lesedi Nuclear Services in South Africa.
In Egypt, this solution will reduce plastic pollution. The North African country generates an average of 270,000 tonnes of plastic waste out of the 570,000 tonnes that cross the Mediterranean every year.
Pyrolysis, or how to convert waste into fuel
Pyrolysis has more than one trump card up its sleeve. As one of the three main thermochemical conversion processes, it can convert plastic and tyre waste into low-carbon liquid fuels (diesel, aviation fuel, hydrogen). Stellar3, a US waste conversion company, has been trialling the process since 2021, focusing on modular applications. “During the thermochemical process, plastic is heated, extruded and fed directly into an oxygen-free pyrolysis furnace where the decomposition process releases hot gases and cools them. Pyrolysis oil (2,831 litres of oil per tonne of plastic waste processed) is formed from the condensed gases, and the non-condensable gases are used as fuel for the burners, so the process requires no external energy once it’s running,” explains Stellar3 CEO and founder Dan Nienhauser.
According to him, producing diesel via pyrolysis could reduce the greenhouse gas (GHG) emissions required to extract the oil from the ground, transport it to a ship, ship it to a refinery, refine it into naphtha, ship the naphtha to a country, ship the naphtha to a distribution point and ship the diesel to an airport where it is ultimately used by 40 to 60%. And between 30% and 50% for hydrogen, adds the expert. But there’s still time to wait, because the company, based in Phoenix, Arizona in the United States, is in the middle of a major expansion phase.
Stellar3 plans to inaugurate its first plants in Africa in December 2023. “Between now and 2035, we could save more than 40 million tonnes of CO2 equivalent by building 200 new plants around the world, including on the African continent”, explains Dan Nienhauser.
The Canadian company Anaergia has decided to optimise anaerobic digestion by modernising existing digesters.
“Omnivore is our advanced approach to high-solids anaerobic digestion. It can digest just about anything organic, from food waste and wastewater solids to animal manure, to produce three times as much biomethane,” says the company, which was founded in 2010 and is headquartered in Burlington in the United States of America.
An approach that reduces methane emissions
Recycling plants equipped with Omnivore technology can also co-digest fats, oils, food waste, source-separated organic matter, the organic fraction of municipal solid waste, high-resistance industrial waste and industrial wastewater.
Pepsico Johannesburg’s future food waste-to-energy plant, located on the Simba Chips site, will use this technology. With a capacity of 11,500 tonnes a year, it will convert food waste, frying waste and sewage sludge into electricity via an 800 kW power station, as well as fertiliser for Pepsico’s plantations. The aim of the American soft drinks and food giant is to reduce its methane emissions, one of the causes of global warming, as well as its dependence on the South African public utility Eskom’s network.
In addition to anaerobic digestion, the Canadian supplier of solutions for the production of renewable energy has developed a mechanical-biological treatment (MBT) that guarantees maximum recovery of recyclable materials, the production of clean, green energy and the conversion of nutrients into fertiliser. Its OREX™ organic matter extraction solution, meanwhile, extracts more than 90% of putrescible organic matter from mixed municipal solid waste.
Swiss companies operating in Africa are also looking to boost their efficiency in solid waste management. This is the case of Renergon International AG, which has developed a dry fermentation or methanisation technology to transform organic waste into biogas.
A more economical alternative to wet fermentation
“Dry fermentation has proved to be the optimum technology for recovering organic waste, which, throughout the world, is mainly in solid, stackable form,” says Renergon. RSD-Renergon Simultaneous Digestion enables biomass to be stacked in the biogas system’s boxes and the acids evacuated to transform them into biogas in the percolate tank, the treatment liquid that contains all the micro-organisms, nutrients and buffer substances essential to the biogas process.
The biogas formed in the fermentation boxes and the percolate tank is conveyed to the reservoir. The biogas then passes through a treatment system with drying and an activated carbon filter. The resulting condensate is discharged into the percolate circuit. The gas treatment unit makes it possible to meet the gas quality required for the production of electricity and heat through combustion in the cogeneration plant. After around 21 days in the thermophilic hygienisation process (at around 52°C), the fermentation box is reopened and the digestate is spread.
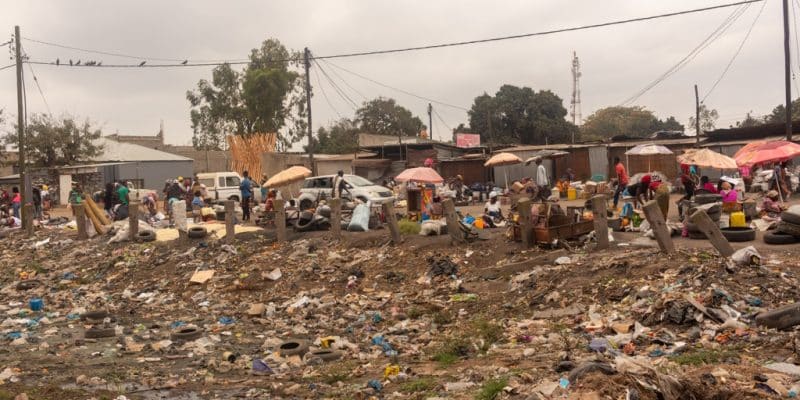
Pyrolysis, anaerobic digestion, dry fermentation. ways to clean up pollution in Africa©Renergon
Dry fermentation of organic waste to produce biogas©Renergon
“This biogas is absolutely neutral in terms of emissions and avoids climate-damaging methane emissions from landfill sites. What’s more, the fertiliser produced by this process improves soil structure and increases the proportion of humus on cultivated land. This accumulation of humus considerably improves the water-holding capacity of the soil, preventing crop losses of over 70% in periods of drought”, says Renergon.
EnviroTaqa for Sustainable Environmental Services & Renewable Energy will be the first company in Africa to produce biogas from dry fermentation. In September 2020, the Egyptian company signed a partnership agreement with Renergon to replicate its biogas production technology in the land of the pharaohs.
To get the most out of organic waste, Veolia has opted instead to develop insect-based bioconversion. “This solution makes it possible to transform food by-products and agricultural waste in its raw liquid or solid state into proteins for animal feed, via the production of insects”, reveals the French multinational.
And what if insects were a solution for the future?
When black soldier fly larvae come into contact with organic by-products, they feed on them and grow. Once they reach a sufficient size, they are washed, dehydrated, ground and transformed into oil and protein concentrate.
According to the Aubervilliers-based company, 1 kg of black soldier fly eggs produces six tonnes of larvae in 10 days, which, once fed with organic matter, will be used as protein for fish, poultry and pork, replacing fish meal.
To date, Veolia’s solution has only been tested in Malaysia. If widely adopted, it could make it possible to feed 10 billion people worldwide by 2050, using less water, less energy and less land, and producing sustainable proteins for animal feed, says Veolia. He adds that 70% more animal protein will be needed to meet global demand.
This is also the approach taken by Kenyan start-up Ecodudu, which for several years has been producing feed for aquaculture and for the nutrition of many other animal species. The feed produced by the young company has a higher protein density than soya beans. As adult larvae, the flies are dried and supplied in bulk to animal feed manufacturers for commercial use. At the end of the process, the waste is transformed into an organic fertiliser called ‘Shamba Mix’. As well as being a protein product, frass, a bioconversion co-product, is an excellent organic fertiliser, restoring soil organic matter and replacing chemical fertilisers.
There is no doubt that popularising these different solid waste management technologies, whether bioconversion, pyrolysis, anaerobic digestion or dry fermentation, will help to improve life in the future. But these technologies will have to be accessible and easy to use, especially in a continent like Africa where there is a huge need for funding and skilled labour.
Source: Afrik 21
Read here.
buying cheap lisinopril without prescription
They’ve revolutionized international pharmaceutical care.